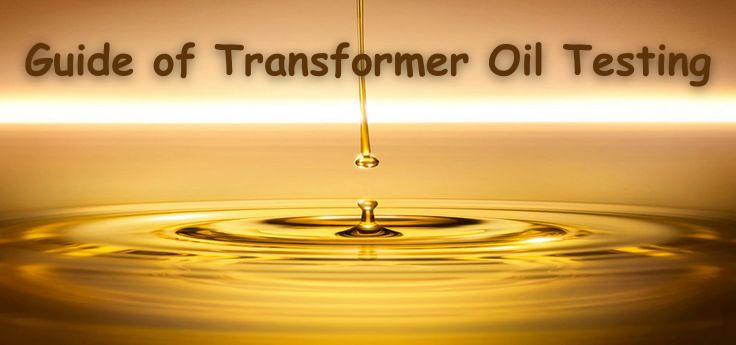
Introduction
The fault free operation of power transformers is a factor of major economic importance and safety in power supply utilities and industrial consumers of electricity.
In the current economic climate, Industries/Supply Utilities tighten their control on capital spending and make cutbacks in maintenance, an increased awareness is placed on the reliability of the existing electric power supply. Downtime is at a premium. Often, the loading is increased on present units, as this will defer purchasing additional plant capacity. Thus the stress on the transformer increases. The net total effect of the thermal, electrical, and mechanical stress brought on by increased service needs to be monitored to ensure reliability
Regular sampling and testing of insulation oil taken from transformers is a valuable technique in a preventative maintenance program. If a proactive approach is adopted based on the condition of the transformer oil, the life of the transformer can be extended.
Why is Transformer Oil Testing Important?
- Determine essential electrical properties of transformer oil
- Identify if a certain oil is suitable for future use
- Detect whether regeneration or filtration is needed
- Reduce oil costs and enhance component life
- Prevent untimely failures and maximize safety
Some Important Transformer Oil Tests & their Significance
Dielectric Strength / Breakdown Voltage Test
The dielectric strength of an insulating oil is a measure of the oil’s ability to withstand electrical stress without failure. The test involves applying an AC voltage at a controlled rate to two electrodes immersed in the insulating fluid. The gap is a specified distance. When the current arcs across this gap the voltage recorded at that instant is the dielectric strength breakdown strength of the insulating liquid. Contaminants such as water, sediment, and conducting particles reduce the dielectric strength of an insulating oil. A combination of these tends to reduce the dielectric strength to a greater degree. Clean dry oil has an inherently high dielectric strength but this does not necessarily indicate the absence of all contaminants, it may merely indicate that the amount of contaminants present between the electrodes is not large enough to affect the average breakdown voltage of the liquid.
Authorities now agree that careless sampling and testing technique has been the source of 99 percent of “bad dielectric readings”
Specific Resistance / Resistivity Test
This is another important property of transformer oil. The specific resistance of oil is a measure of DC resistance between Two opposite sides of one cm block of oil. Its unit is ohm-cm at a specific temperature. With the increase in temperature, the resistivity of oil decreases rapidly.
Just after charging a transformer after a long shutdown, the temperature of the oil will be at ambient temperature, and during full load, the temperature will be very high and may go up to 90 °C at an overload condition. So resistivity of the insulating oil must be high at room temperature and it should have good value at high temperatures as well.
That is why the specific resistance or resistivity of transformer oil should be measured at 27°C as well as 90°C. The minimum standard specific resistance of transformer oil at 90°C is 35 × 10 ohm–cm and at 27°C it is 1500 × 10 ohm–cm.
Dissipation Factor / Tan Delta Test
The Dissipation test measures the leakage current through an oil, which is the measure of the contamination or deterioration i.e. Reveals the presence of moisture resin, varnishes, or other products of oxidation oil or of foreign contaminants such as motor oil or fuel oil. The test is not specific in what it detects i.e. is more of a screening test
Water Content Test
Water, in minute quantities, is harmful to power equipment because it is attracted to the places of greatest electrical stress and this is where it is the most dangerous. Water accelerates the deterioration of both the insulating oil and the paper insulation, liberating more water in the process (heat catalyzed). This is a never-ending circle and once the paper insulation has been degraded (loss of mechanical strength) it can never (unlike the oil) be returned to its original condition.
Origins of Water
Water can originate from two sources.
Atmospheric
Via the silica gel breather (dry silica gel is always blue).
Via leaks into the power equipment, i.e. bad casketing, cracked insulation, a loose manhole cover, a
ruptured explosion diaphragm, etc. (if oil can get out, water can get in).
Internal Sources
Paper degradation produces water.
Oil degradation produces water.
Wet insulation contaminates the oil, (temperature dependent)
Acidity or Neutralisation Number Test
Acids in the oil originate from oil decomposition/oxidation products. Acids can also come from external sources such as atmospheric contamination. These organic acids are detrimental to the insulation system and can induce corrosion inside the transformer when water is present. An increase in the acidity is an indication of the rate of deterioration of the oil with SLUDGE as the inevitable by-product of an acid situation that is neglected. The acidity of oil in a transformer should never be allowed to exceed 0.15mg KOH/g oil. This is the CRITICAL ACID NUMBER and deterioration increases rapidly once this level is exceeded.
Interfacial Tension(IFT) Test
The Interfacial Tension (IFT) measures the tension at the interface between two liquids (oil and water) which do not mix and is expressed in dyne/cm. The test is sensitive to the presence of oil decay products and soluble polar contaminants from solid insulating materials. A good oil will have an interfacial tension of between 40 and 50 dynes/cm. Oil oxidation products lower the interfacial tension and have an affinity for both water (hydrophilic) and oil. This affinity for both substances lowers the IFT. The greater the concentration of contaminants, the lower the IFT, with a badly deteriorated oil having an IFT of 18 dynes/cm or less
Flash Point Tests
The flash point of transformer oil is the temperature at which oil gives enough vapors to produce a flammable mixture with air. This mixture gives a momentary flash on the application of flame under standard conditions. Flashpoint is important because it specifies the chances of fire hazards in the transformer. So it is desirable to have a very high flash point of transformer oil. In general, it is more than 140 °C
Pour Point Of Test
It is the minimum temperature at which oil starts to flow under standard test conditions. The pour point of transformer oil is a valuable property mainly in places where the climate is icy. If the oil temperature falls below the pour point, transformer oil stops convection flowing and obstructs cooling in a transformer. Paraffin-based oil has a higher pour point, compared to Naphtha based oil, but in India like country, it does not affect the use of Paraffin oil due to its warm climate condition. The Pour Point of transformer oil mainly depends upon the wax content in the oil. As Paraffin-based oil has more wax content, it has a higher pour point.
Viscosity Of Test
In a few words, the viscosity of transformer oil can be said to be the resistance of flow, in normal conditions. Resistance to the flow of transformer oil means obstruction of the convection circulation of oil inside the transformer. Good oil should have a low viscosity so that it offers less resistance to the conventional flow of oil thereby not affecting the cooling of a transformer. The low viscosity of transformer oil is essential, but it is equally important that the viscosity of oil should increase as little as possible with a decrease in temperature. Every liquid becomes more viscous if the temperature decreases
Dissolved Gas Analisis Test
Transformers are vital components in both the transmission and distribution of electrical power. The early detection of incipient faults in transformers is extremely cost-effective by reducing unplanned outages. The most sensitive and reliable technique used for evaluating the health of oil-filled electrical equipment is dissolved gas analysis (DGA). Insulating oils under abnormal electrical or thermal stresses break down to liberate small quantities of gases. The qualitative composition of the breakdown gases is dependent upon the type of fault. By means of dissolved gas analysis (DGA), it is possible to distinguish faults such as partial discharge (corona), overheating (pyrolysis), and arcing in a great variety of oil-filled equipment. Information from the analysis of gasses dissolved in insulating oils is valuable in a preventative maintenance program. A number of samples must be taken over a period of time for developing trends. Data from DGA can provide Advance warning of developing faults. A means for conveniently scheduling repairs. Monitor the rate of fault development
NOTE: A sudden large release of gas will not dissolve in the oil and this will cause the Bocholt relay to activate
Origin Of Gases In Transformer Oil
Fault gases are caused by corona (partial discharge), thermal heating (pyrolysis), and arcing.
Partial Discharge
A fault of low-level energy usually occurs in gas-filled voids surrounded by oil-impregnated material. The main cause of decomposition in partial discharges is an ionic bombardment of the oil molecules. The major gas produced is Hydrogen. The minor gas produced is Methane
Thermal Faults
A small amount of decomposition occurs at normal operating temperatures. As the fault temperature rises, the formation of the degradation gases changes from Methane (CH4) to Ethane (C2H6) to Ethylene (C2H4). A thermal fault at low temperature (<300deg/C) produces mainly Methane and Ethane and some Ethylene. A thermal fault at higher temperatures (>300deg/C) produces Ethylene. The higher the temperature becomes the greater the production of Ethylene.
Arcing
A fault is caused by a high energy discharge. The major gas produced during arcing is acetylene. Power arcing can cause temperatures of over 3000deg/C to be developed.
NOTE: If the cellulose material (insulating paper etc.) is involved, carbon monoxide and carbon dioxide are generated.
A normally aging conservator-type transformer having a CO2/CO ratio above 11 or below 3 should be regarded as perhaps indicating a fault involving cellulose provided the other gas analysis results also indicate excessive oil degradation
Transformer oil carries useful information about the condition of the transformer. Like blood in the human body. Degradation of paper & Internal fault.
An important part of the health monitoring of the Transformer is oil sampling
Transformer oil is an essential component of power transformers, and its proper maintenance is crucial for the longevity and efficiency of the transformer. One of the key elements of transformer oil maintenance is regular oil sampling. The process of transformer oil sampling is relatively simple, but it’s important to follow the correct procedure to ensure accurate and reliable results.
Transformer Oil sample container size and its material
Most of the time, the size of the container used to take a sample of transformer oil depends on how much oil is needed for analysis. In general, a minimum of 1000 mL of oil is needed for analysis. Some laboratories may specify a larger container size based on their testing requirements. To make sure that the sample is representative of the whole amount of oil, it is important to follow the laboratory instructions for the right size of the container.
The material of the container is also an important consideration. The container should be made of a material that is compatible with the transformer oil, such as Aluminium, glass, or Stainless steel. People often choose Stainless steel containers because they don’t react with the transformer oil and can handle high temperatures. You can also use Aluminium, it is important to use a container that is properly sealed with a tight-fitting lid that can be securely fastened to avoid any leakage during transport. Additionally, the container should be handled carefully to avoid any spills or contamination.
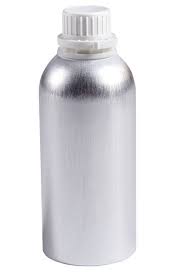

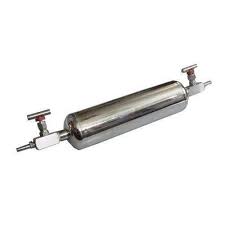
Don’t use plastic bottles because they react with the transformer oil and cannot handle high temperatures. They may affect transformer oil test results & you cannot monitor your transformer properly
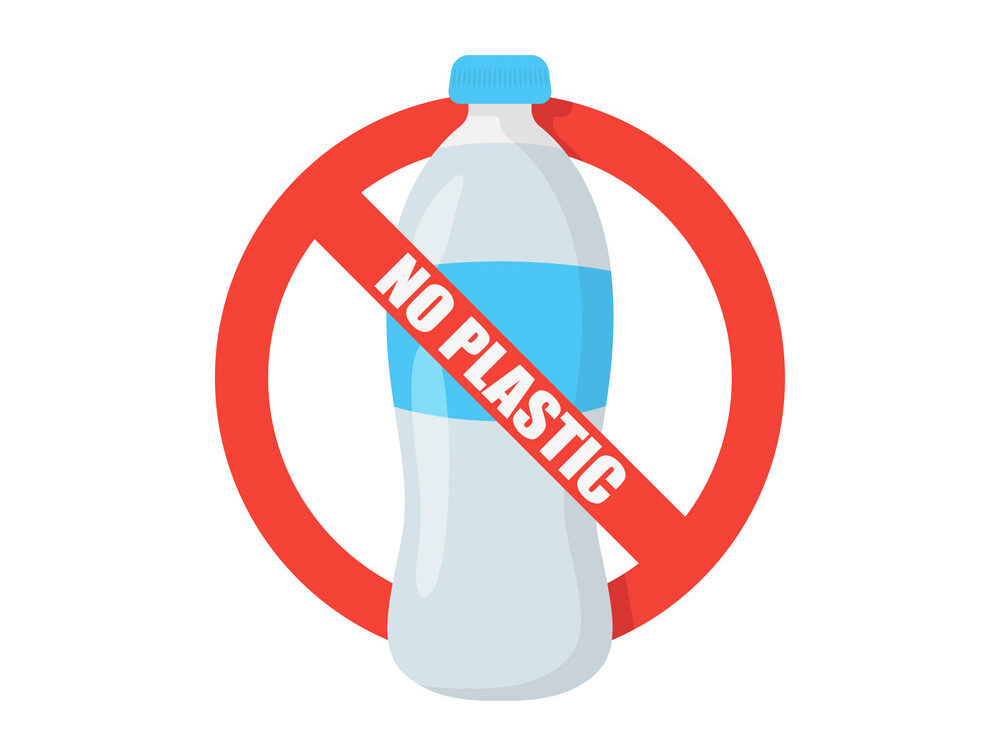