What is Transformer Oil Testing?
Transformer oil testing is analogous to blood testing for people. Transformer oil testing is
one of the most well-known and effective loss prevention strategies, and it needs to be a part
of each organization’s maintenance schedule. In addition to serving as an early warning
system, it also enables us to assess the transformer’s internal condition without interfering
with its normal operation.
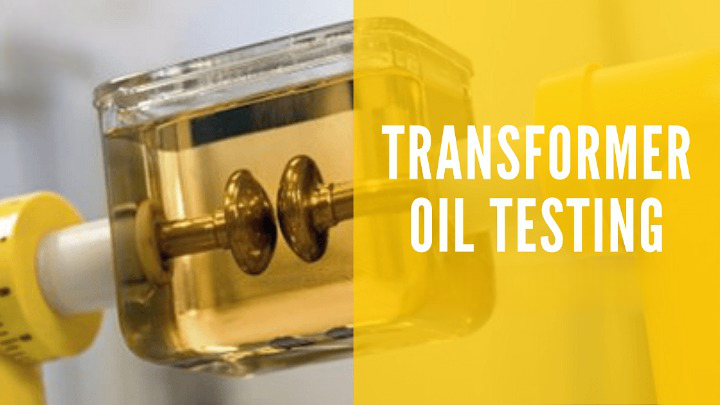
Transformer oil testing, when done on a regular basis, offers the maintenance staff
time to set priorities, allocate tasks, and arrange for outside vendors to service the
transformers, or even order the necessary supplies and parts.
Transformer oil needs to be tested to make sure it meets modern requirements. International
standards,
Why Transformer Oil Testing is Important?
It’s important to recognize that the fluid used in transformers serves as both a heat-transfer
medium and a component of the insulating system. It is necessary for the safe operation of
the transformer and helps to maintain the internal temperature of the transformer. Therefore,
it is important to regularly test the oil to see if the insulating oil is able to execute its
function as an insulant.
Testing of transformer oil is essential for:
Identify the essential electrical characteristics of transformer oil.
Determine whether a particular oil is suitable for usage future.
Identify the requirement for filtration.
Boost component life and cut oil expenses
Maximize safety and avoid untimely failures
What are all the Factors to be considered for Transformer Oil testing?
The following are the main characteristics to consider while doing a transformer oil test:
Dielectric Breakdown Voltage
Moisture Content test
Dielectric Dissipation Factor (TAN DELTA) Test
Resistivity test
Interfacial tension test
Visual examination
Acid number
Flash Point test
Pour Point test
Viscosity Test
Density test
Dissolved Gas Analysis test
These tests will establish a baseline of the qualities that need to be checked on a regular
basis and help to determine whether the oils are clean. Despite the abundance of available
tests, their cost makes them unaffordable.
The power and voltage have an impact on the recommended frequency. The frequency must
be increased if the test findings raise any warning signs. Even though testing is expensive, it
should still be weighed against the cost of replacing a transformer and the downtime caused
by a lost transformer.
Sr. No. | Test Parameter | Test Standard |
1 | Water Content | IEC 60814:1997 / IS 13567:2018 |
2 | Breakdown Voltage | IEC 60156:1995 / IS 6792:2017 |
3 | Acidity | IEC 62021:2003 / IS 1448 (P-2): 2007 |
4 | Interfacial Tension | ASTM D971:2012 / IS 6104:1971 |
5 | DDF/ Tan Delta @90°c | IEC 60247:2004 / IS 6262:1971 |
6 | Resistivity @90°c | IEC 60247:2004 / IS 6103:1971 |
7 | Sediments & Sludge | IS 1866:2017 (Annexure–C) |
8 | Flash Point | ISO 2719:2016 /IS 1448(P-21):2019 |
9 | Density | IS 1866-2017 |
10 | Pour point | IS 1448 (P-10 S-2):2013 / ISO 3016: 2019 |
11 | Kinematic viscosity | IS 1448 (P-10 S-2) :2013 / ISO 3016: 2019 |
12 | Physical condition & appearance test | IS 1866-2017 |
13 | Dissolved Gas analysis test | IS 10593 & IS 9434-1992 |
Various Transformer Oil Testing Methods
Transformer oil can be tested using a variety of techniques, which include:
Physical condition & appearance test
Dielectric Breakdown Voltage (BDV Test)
Color Analysis
Dissolved Gas Analysis (DGA Test)
Flash Point or Fire Point
Furan Analysis
Interfacial Tension
Neutralization Number or Acid Number
Moisture Content
Resistivity
Pour Point
Density
Physical condition & appearance test:
TEST: One of the initial tests that are typically performed in a lab is a visual inspection,
which is done by beam of light through it to verify transparency and spot foreign particles.
RESULT: If the oil is contaminated, it will show through as cloudiness, poor transparency,
or the detection of foreign particles.
Dielectric Breakdown Voltage (BDV Test):
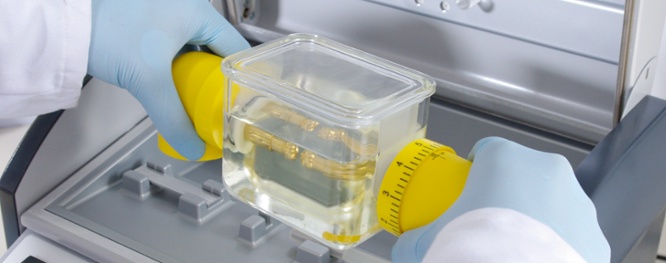
TEST: With this test, the insulating oil’s dielectric strength is evaluated; in other words, we
measure the voltage at which the oil fails electrically, which is a reliable indicator of the
oil’s moisture content. The oil is tested by simply placing a sample between two electrodes
and progressively applying voltage until the electrodes reach a sufficient potential and begin
to conduct through the oil. This value is known as the breakdown voltage of the oil.
RESULT: The transformer oil must have a minimum dielectric strength of 40 kV according
to the international standard, which is also used for this test. In kV, the BDV is measured.
Color Analysis:
TEST: As the names indicate, the oil sample is compared to an earlier sample taken from
the same transformer to look for oil darkening. A set of color standards are compared with
the numerical value between 0 and 5 assigned to the oil’s color after it is measured for
light transmission.
RESULT: It is safe to presume that internal arching has occurred in the transformer or that
there has been a notable discoloration of the oil if that arching occurred.
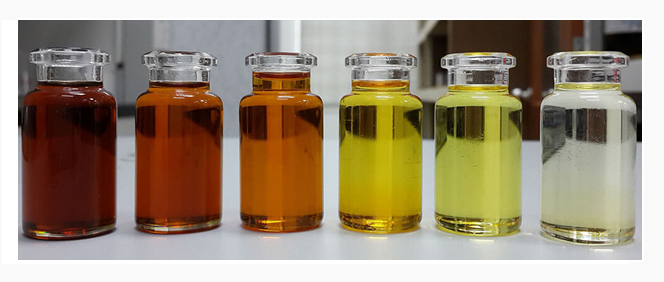
Dissolved Gas Analysis Test (DGA Test):
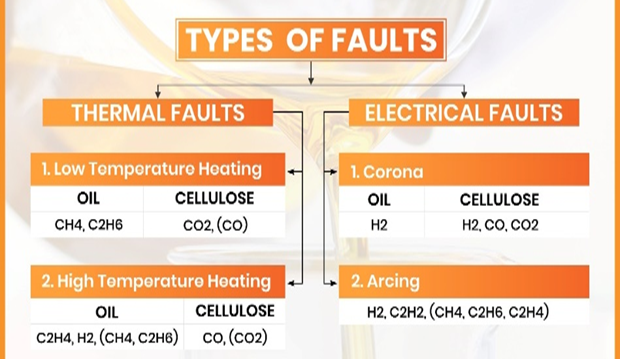
THERMAL FAULT: At standard working temperatures, a minor amount of degradation takes place. The generation of the degradation gases shifts from Methane (CH4) to Ethane (C2H6) to Ethylene as the fault temperature rises (C2H4). Methane, ethane, and a small amount of ethylene are the major products of a thermal fault at low temperatures (300 C). Ethylene is produced via a thermal fault at temperatures higher than 300 °C. The more heated the environment, the more ethylene is produced.
- Typically, overheating windings cause the cellulose insulation to thermally decompose. In this instance, DGA data demonstrate elevated carbon oxide concentrations, carbon monoxide, and carbon dioxide. Methane and ethylene are occasionally found in higher concentrations.
- Methane, ethane, and ethylene are produced when oil overheats as a result of the heat-induced breakdown of the liquid.
ELECTRICAL FAULT: An electrical fault releases energy that causes the chemical bonds in the insulating fluid to be broken. These elements readily recreate the fault gases after the bonds are disrupted. Because the energies and speeds at which the gases are generated vary for each gas, it is possible to analyse the gas data to identify the type of faulting activity occurring within the electrical equipment.
- Elevated hydrogen in a DGA will reveal the presence of a corona, a partial discharge.
- Even modest quantities of acetylene are a sign of arcing, the most serious condition in a transformer
TEST: This test involves collecting an oil sample in a glass syringe that has all of the fault gases dissolved in it. The oil sample is then sent to a lab for analysis, which detects the different gas ppm levels that are present in the insulating oil.
RESULT: Different gases that have been dissolved in the oil suggest various forms of thermal and electrical stress within the transformer.
REFERENCE: International Standard ASTM D3612.
Flash Point or Fire Point:
TEST: It is the lowest temperature at which heated oil begins to emit enough vapour to combine with air to generate a flammable moisture.
RESULT: The purpose of this test is to determine the oil’s volatility.
Furan Analysis:
TEST: High-performance liquid chromatography, or HPLC, is used to make measurements in this test, which is conducted in accordance with ASTM
RESULT: This test enables us to identify the presence of cellulosic material, whether it originates from the press board or the paper insulation of the windings, which produces furanic chemicals in the oil.
Interfacial Tension:
TEST: This test helps in determining the presence of soluble pollutants and oxidation by-products in the insulation oil. An increasing value denotes greater contamination, and the unit of measurement is mN/m.
RESULT: The interfacial tension of water and oil is evaluated in this test.
Neutralization Number or Acid Number:
TEST: This test, is performed to find out how much acid is present in the oil. In new transformer oil, there is typically no acid content, however this could change due to oxidation and contamination.
RESULT: The test involves calculating how much potassium hydroxide (KOH, expressed in mg) is needed to neutralise the acid in one gram of oil.
Moisture Content:
TEST: It’s important to note that the test is prefer to have as little moisture in the oil as possible because greater moisture weakens the insulating dielectric strength, which increases the risk of flashovers. Special glass bottles are used to collect the oil, which are subsequently sent to a lab for analysis. These amber glass bottles have a cone cap and can’t be used again.
RESULT: By dividing the weight of the moisture by the weight of the oil, the amount of moisture in the oil can be estimated. The allowable value for standard mineral oil is 20 ppm.
Resistivity:
TEST: This test, as its name suggests, is utilised to ascertain the oil’s resistivity or helps in comprehension of its insulating characteristics.
RESULT: A low resistivity indicates that the oil has a large concentration of free ions, which suggests that the oil contains conductive contaminants. Ohms is the unit of measurement
Pour Point:
TEST: This test is highly essential, especially if the transformer is situated in an extremely cold environment.
RESULT: In this test, the lowest temperature at which the oil will flow is measured, ensuring that the oil will circulate and fulfil its function as insulation.
Density:
TEST: Relative density can be used to determine if ice will float on the oil in extremely cold climates. This test makes use of a hydrometer at a reference temperature to estimate density, also known as specific density.
RESULT: If the test yields a high number, it means the oil has the capacity to hold water in suspension.